In partnership with MiCodmc, a selection of establishments ripe for discovery during the 63rd edition of the Salone del Mobile.Milano, from 8th to 13th April
Tipstudio and De Castelli: affinities between metal and craft skills
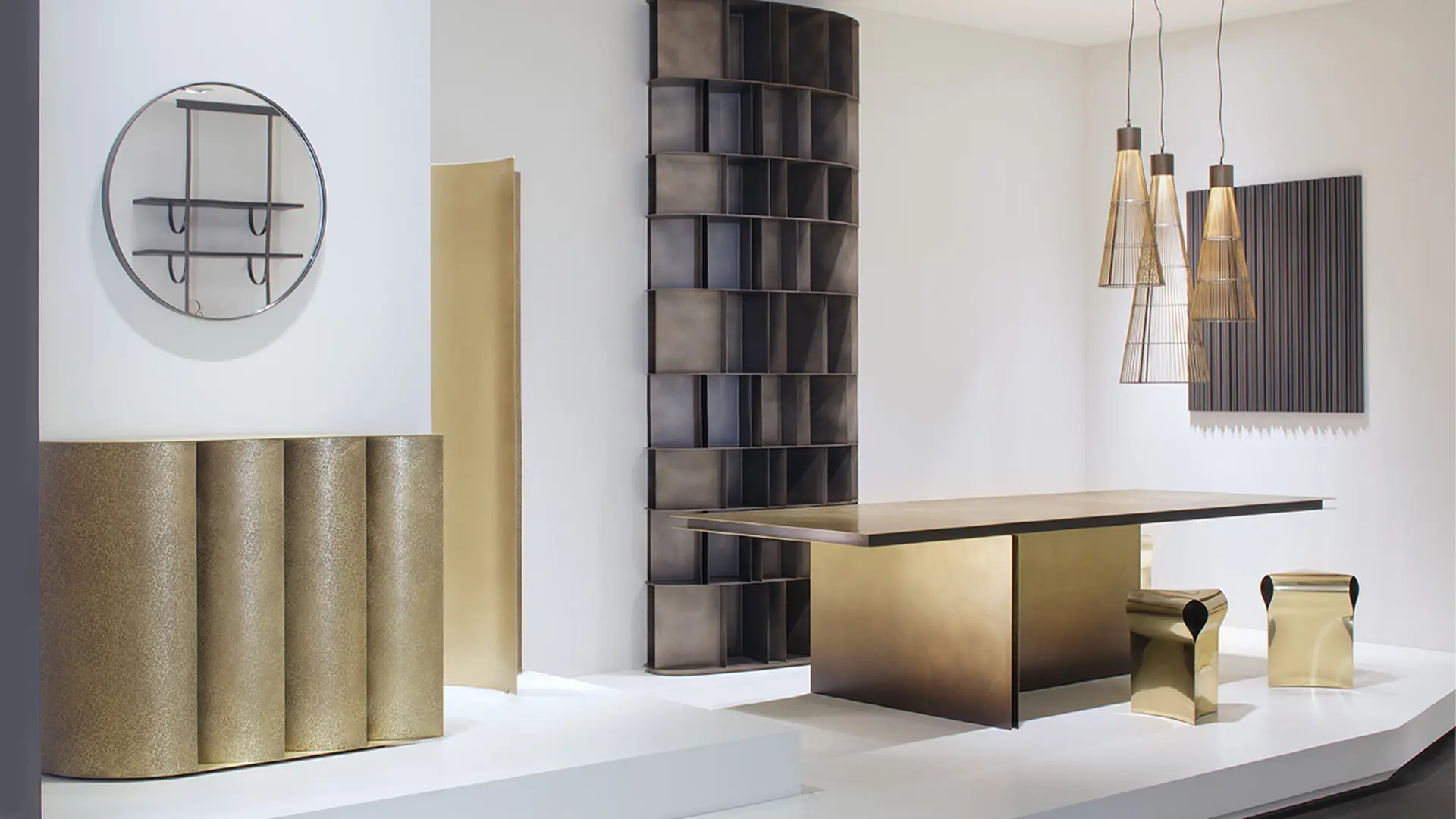
De Castelli at Salone del Mobile.Milano 2023, ph. Alberto Parise
The excitement of the product? It’s created through research into materials. As in Monolìte and Sinestesia, which enhance the solidity and sensuousness of brass, inspired by natural erosions
Scouting the freshest collaborations identified at the latest edition of the Salone del Mobile.Milano. Among the new faces are Imma Matera and Tommaso Lucarini. Together since 2017 as TIPSTUDIO, based in Florence and Pietrasanta, they conduct research into materials with a highly poetic touch. In their first joint venture with the Treviso-based company De Castelli, active in metalworking for four generations, combining craft skills with industrial processes, TIPSTUDIO presented two furnishings in brushed brass with contrasting rough and irregular finishes on the inner parts, smooth and polished on the exteriors: Monolìte, a screen consisting of two symmetrical concave brass sheets that create a vertical architectural interplay, and Sinestesia, a console table with strongly sensuous and sculptural values.
We presented TIPSTUDIO and Albino Celato, CEO of De Castelli, with three quick questions.
We believe that today it’s really crucial to give a deeper value to objects through storytelling, whether it’s embodied in their material qualities and process, or immaterial factors in terms of experience and empathy, which mature with the product to produce objects with a strong identity capable of keeping the story alive.
Our collaboration with De Castelli arose almost spontaneously, naturally, driven by the curiosity on our side to design and explore matter from a different viewpoint. We have a shared affinity based on metal and its expressive qualities.
We discussed the technique for processing semi-finished products, combining our more experimental approach to experience in metal casting with their production and craft capabilities.
We see each project as the result of the process that generated it, the form simply becomes the output of research. We have a vision of the project that creates scope for experimentation and opens up new expressive and emotional worlds. There is a continuous interweaving between self-production and seriality: they’re closely correlated. Self-production is the supreme testing ground, freer as it is often independent and less bound up with productive and commercial logic. The projects that reach companies are then the evolution, the synthesis, of processes, details and research begun in the laboratory.
For instance, in Monolìte and Sinestesia we find an interplay of repetition and reflection, with a more serial character, if you like, that dovetails with the company’s extreme technical craftsmanship. Alike yet different elements are repeated in a delicate spatial interplay of voids and solids.
We pay close attention to the sensory qualities of projects through surface contrasts. Here the experimentation lay in the search for a surface finish that approached the spontaneous, unpredictable behavior of casts. The surface finishes of the products are inspired by the sediments of the molten metal as if they were natural erosions. The hand perceives the transition from smooth to eroded and one can read the three-dimensional movement of erosion on the sheet metal, De Castelli’s distinctive hallmark.
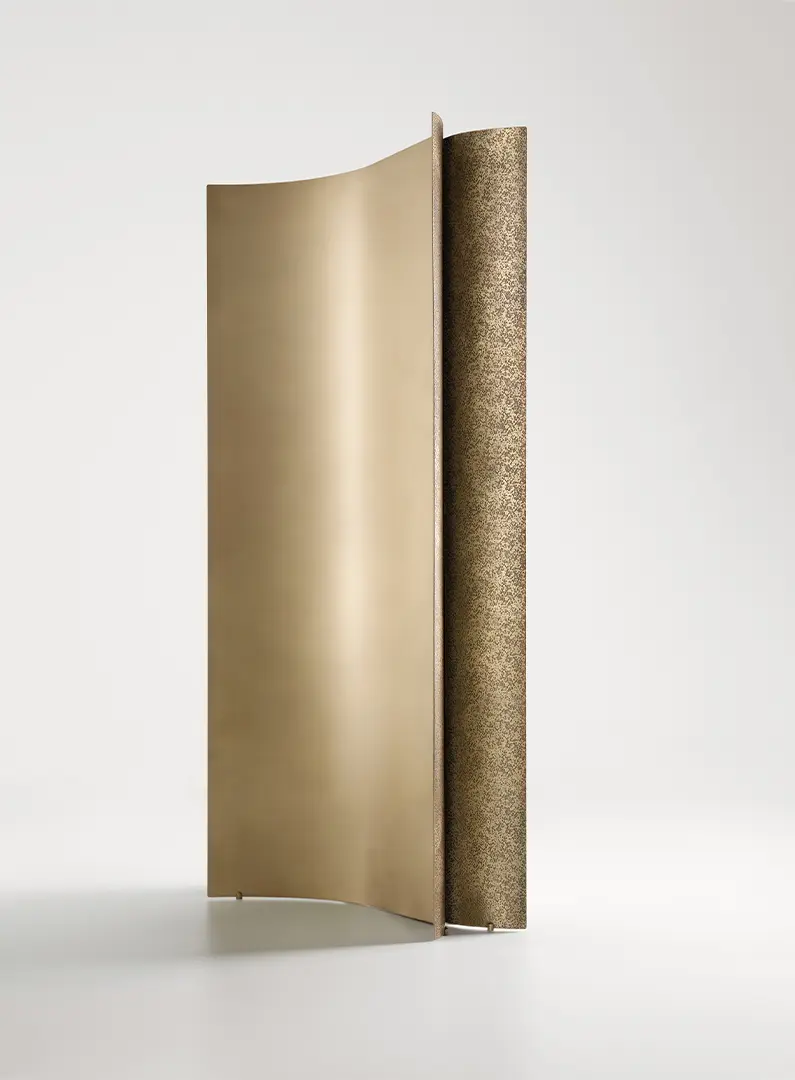
De Castelli, Monolìte, design TIPSTUDIO, ph. Alberto Parise
It is antithesis that enhances the material, with the project evolving and maturing in it. Our way of approaching the project is very closely bound up with our two opposed and complementary personalities, in one case more design-based and conceptual in the other more material and artistic. We were born and raised in contact with marble, metal and ceramic workshops, but at the same time we have a training as designers. We believe that these two factors in our case at a certain point coincide and define a new vocabulary, a new identity capable in some cases of investigating a further artistic logic, but then contained within a design gaze attentive to the technical and productive factors.
We believe that the project creates the context in which we establish a constructive dialogue, a project cultivated by several hands, where history, material and production techniques come together, whether it is a product with a more industrial or craft character.
The collaboration with De Castelli reflects this synergy, a partnership attentive to both crafted and design values, capable of pushing research into the material to its productive limits.
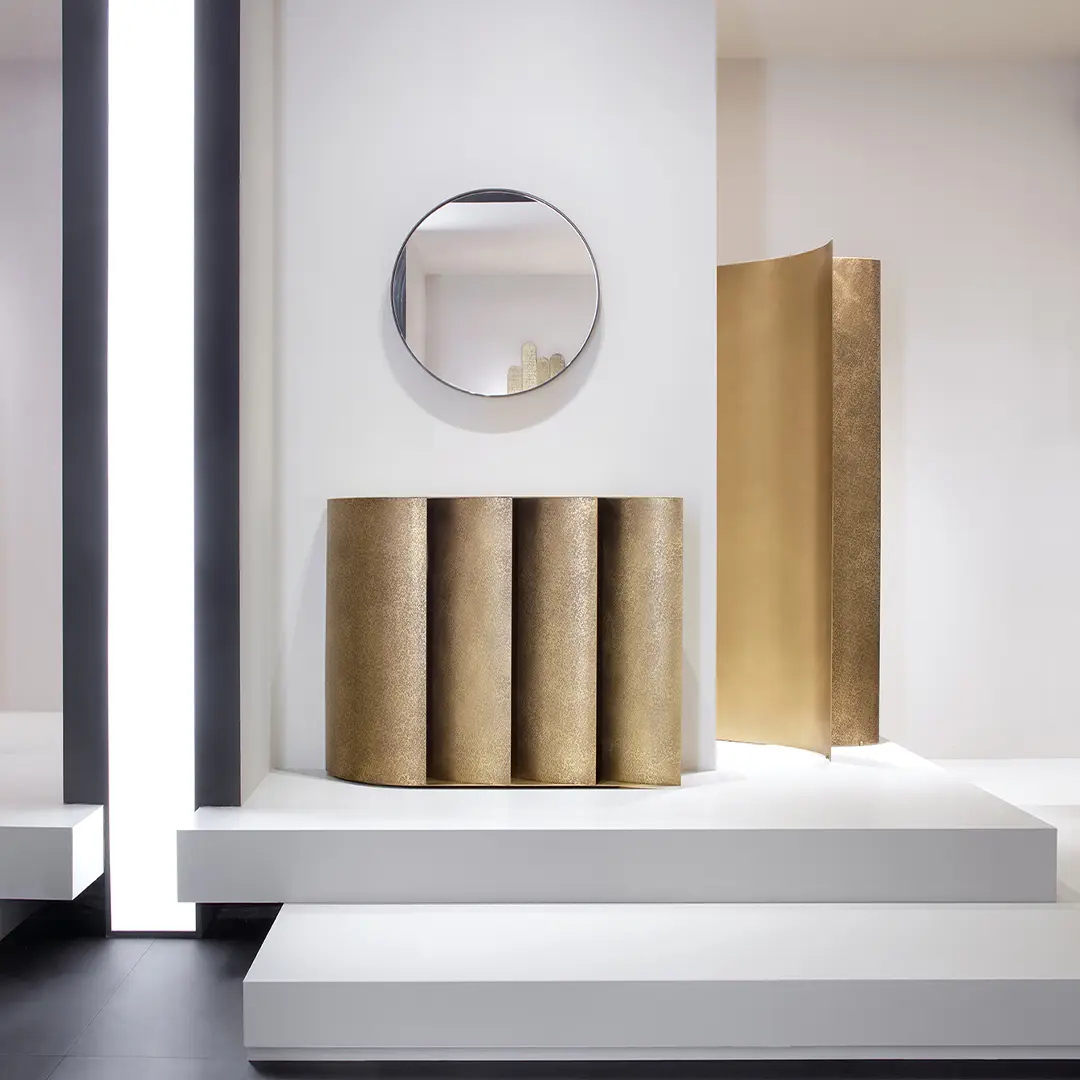
De Castelli at Salone del Mobile.Milano 2023, ph. Alberto Parise
Between De Castelli and TIPSTUDIO there is undoubtedly a natural affinity. Both have a strong interest in and passion for exploring materials, in particular metals, with a sartorial approach, although we differ in the different techniques of fabrication we use. At De Castelli we prefer thick sheet metal, while the TIPSTUDIO duo are heirs to skills bound up with metal casting. The same concept of heritage is a founding characteristic of our company, the heir to four generations of masters in metalworking, as well as TIPSTUDIO, which boasts the backing of one of the most important forges of Pietrasanta. Moreover, both see craftsmanship through a creative and contemporary gaze with the aim of creating new viewpoints and ideas, in which technique and aesthetics interact synergically and each strengthen the other.
Monolìte and Sinestesia are two of the innovations presented at the Salone del Mobile 2023, the result of the intense dialogue between De Castelli and TIPSTUDIO. The proposal that reached us through Imma and Tommaso embodies the suggestions of the Biomorphic research that we presented last year, investigating in a contemporary key the work techniques of sheet-metal beaters from the late 19th century. TIPSTUDIO enthusiastically accepted the project brief by presenting not one, but two products fully expressing the sculptural value and technical approach we requested.
We believe that continuing to entwine our research with the work of Imma and Tommaso could be extremely fruitful, as it would enable both to embrace different viewpoints while maintaining their respective values and principles. From our point of view, exploring the world of metal casting - varying and reinterpreting it in the processing of thick sheet metal - could lead to unexplored regions resulting from connections that appear to be in contrast but actually have close affinities.
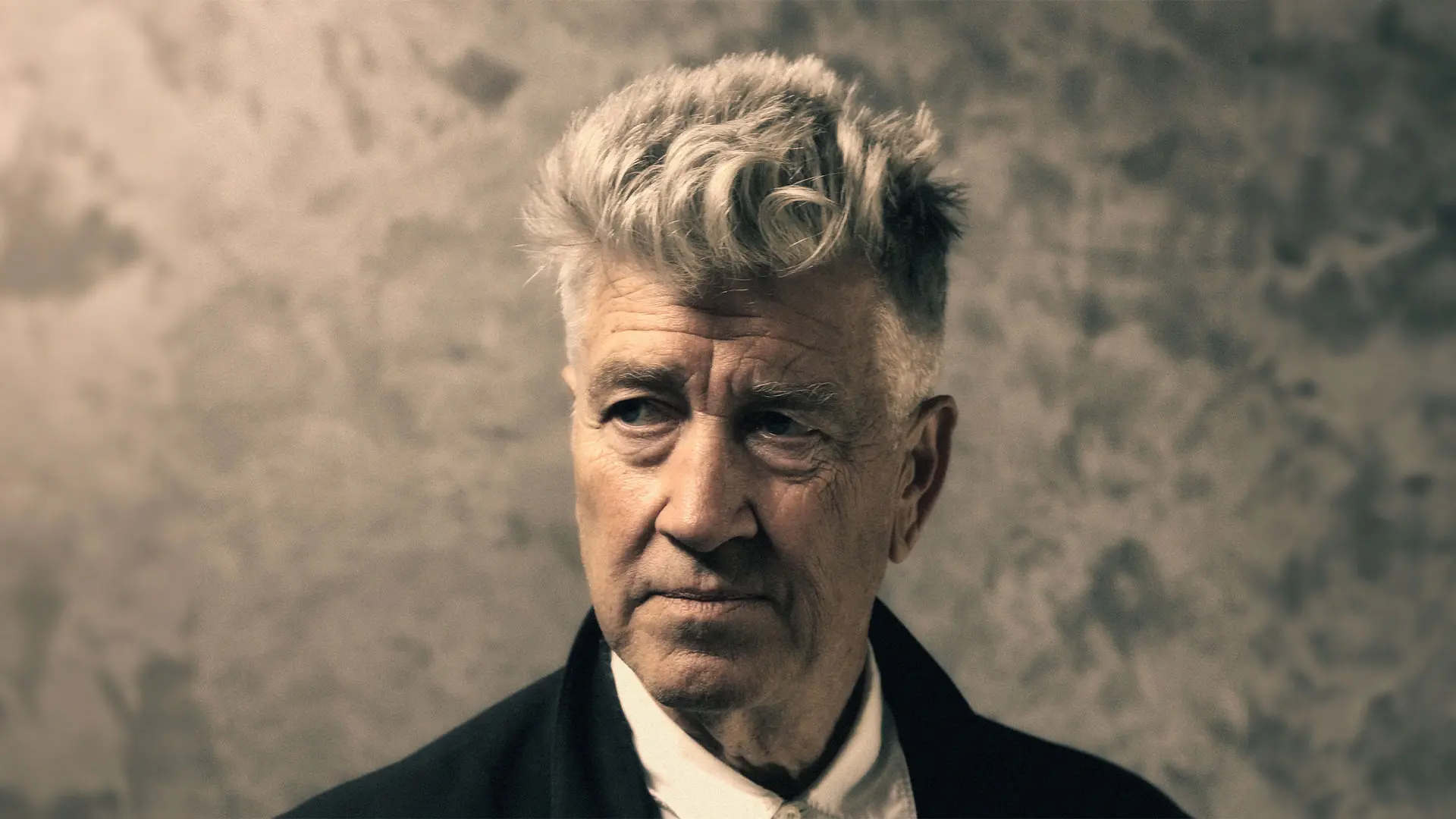
In memoriam: David Lynch
The American director has left us at the age of 78. The Salone del Mobile.Milano had the honor of working with him during its 62nd edition, hosting his immersive installation titled “A Thinking Room”. An extraordinary journey into the depths of the mind and feelings. His vision will continue to be a source of inspiration.