In partnership with MiCodmc, a selection of establishments ripe for discovery during the 63rd edition of the Salone del Mobile.Milano, from 8th to 13th April
CENTO3: a hitherto unseen project by Achille Castiglioni, now in 3D
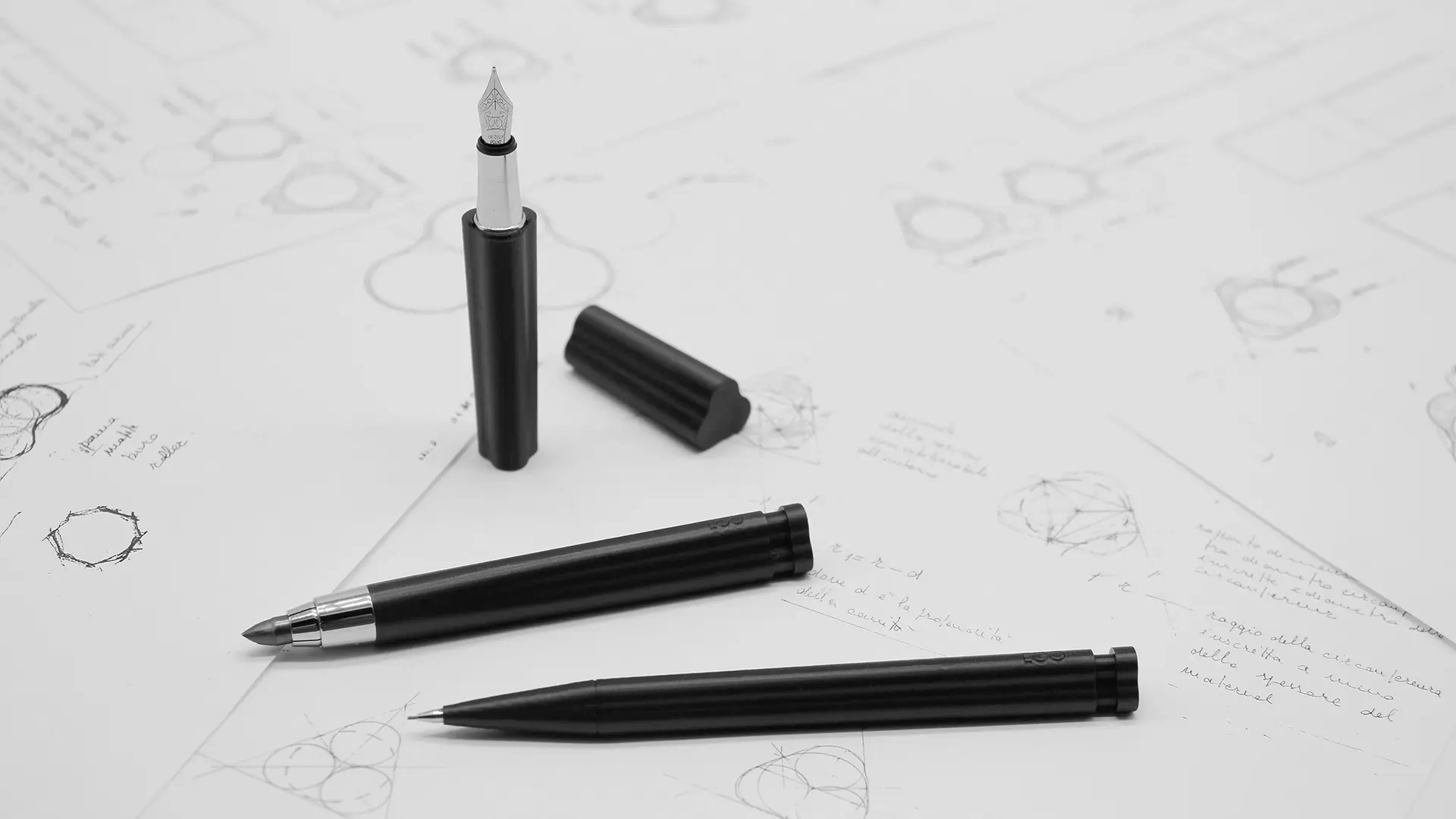
CENTO3, Project Drawings
A writing set devised by the design Master and Gianfranco Cavaglià comes to fruition thanks to the vision of a young design studio in Bologna. Underscoring the importance of these instruments and of intergenerational exchange
Not just lamps, chairs, tables, stools, sanitaryware, cutlery, plates, glasses and even a switch, a peanut dispenser and a whistle – all that was missing was a pen and pencil set. The essential toolkit for an architect, pre-computer at least. It is certainly no coincidence that this extension of the hand and the mind was Achille Castiglioni’s final project, in 2001 – a symbolic passing of the baton to subsequent generations.
Designed with his architect friend Gianfranco Cavaglià, the project was discovered not long ago lodged behind a mirror in his Piazza Castello studio – the headquarters of the Foundation that bears his name since 2012. The project was never brought to completion because the technology of the day would have generated far too much waste material, with significant repercussions on the final price.
It was the Achille Castiglioni Foundation, along with Gianfranco Cavaglià, that set the production of this graphene filament writing set in motion, entrusting the engineering and production to the young Team EGO.M. The name CENTO3 was chosen because the product was presented on the 103rd anniversary of Castiglioni’s birth, on 16th February 2021, and because three fingers are used to hold a pencil, it takes three arches to create the trilobate form of the instruments and because the set consists of three pieces – micro-lead, chubby pencil and fountain pencil. Last September, to mark “supersalone” week, a series of adaptable, interchangeable and coloured accessories was added, in full respect of the original design and with an eye to the future. Lastly, three partners worked on the project, and three generations were involved.
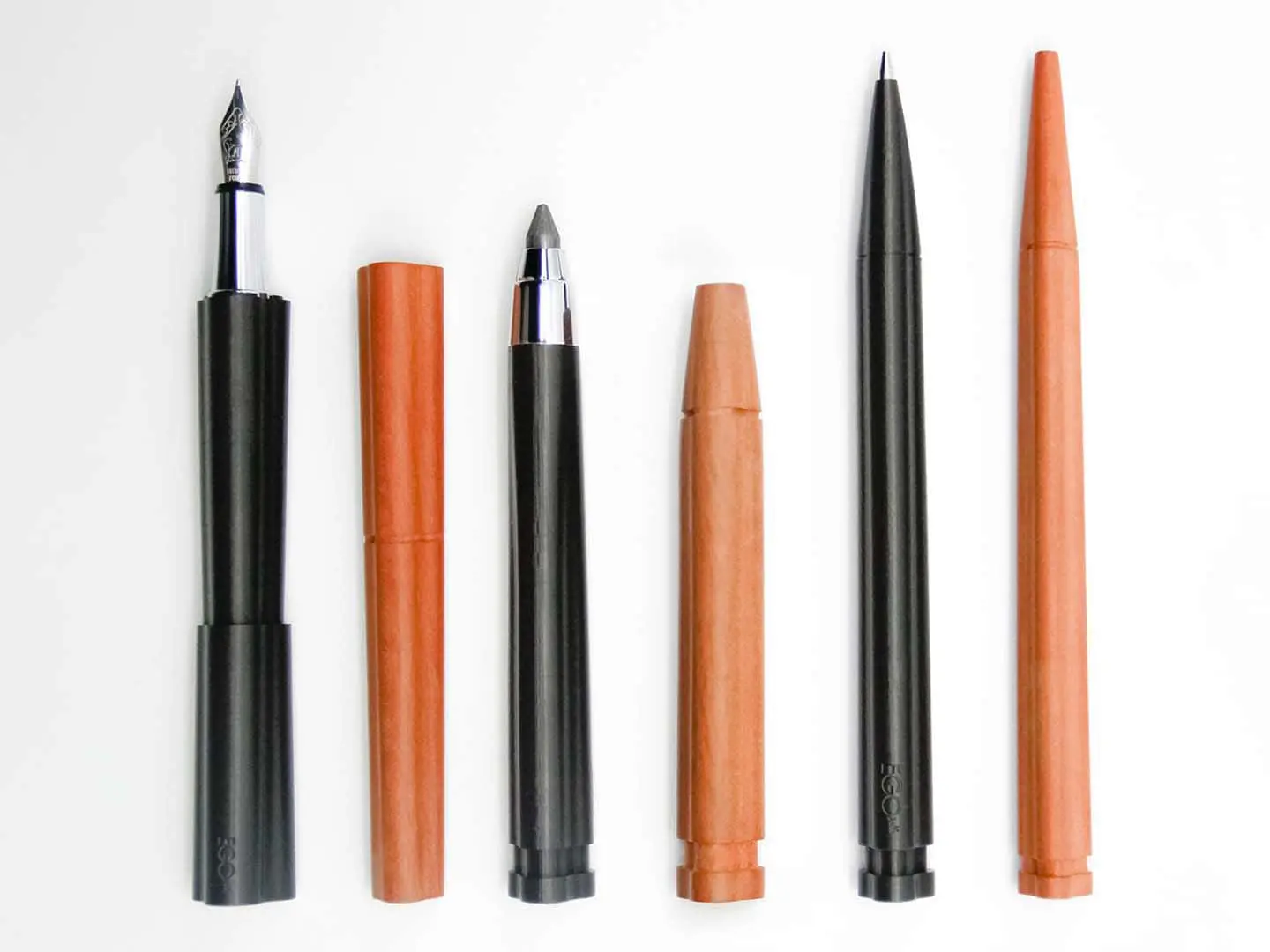
CENTO3 in graphene and non functional wooden prototypes
Gianfranco Cavaglià: There was never cause for discord or disagreement in my lengthy partnership with Achille Castiglioni on our approach to design, which is what we were both most interested in, in our separate academic and professional capacities. Our approach involved research, discussion over possible solutions, never trying to override the other, real dialogue: different points of view became hypotheses to be weighed up and developed. The final result was the previously unpredictable outcome. “Design is always an opportunity for authentic research and sometimes discovery,” Castiglioni was wont to say.
EGO.M is a work group in which the roles are well defined and it has leveraged the enthusiasm over the opportunity provided by this project and the potential of 3D printing, which it handled itself. That made it possible to carry out the project, adhering to the original characteristics while discovering interesting possibilities such as the original finish of the printing process, the texture of the surface of the product achieved without further intervention and, equally the colour deriving from the use of graphene, chosen as the only colour. EGO.M put the same level of commitment into the communication and marketing.
EGO.M: Working with Gianfranco Cavaglià and the Achille Castiglioni Foundation has been, and continues to be, a fruitful exchange of skills and experience, a generational approach of two very different eras to a joint project that has brought them together. So, it was only natural and human that various differences of thought and viewpoint cropped up during the lengthy development stage; these were always resolved with constructive mediation and interest in each other’s points of view. An intelligent and respectful balance of everybody’s positions, a combination of scrupulous design and innovative decision-making, which have informed the CENTO3 writing set.
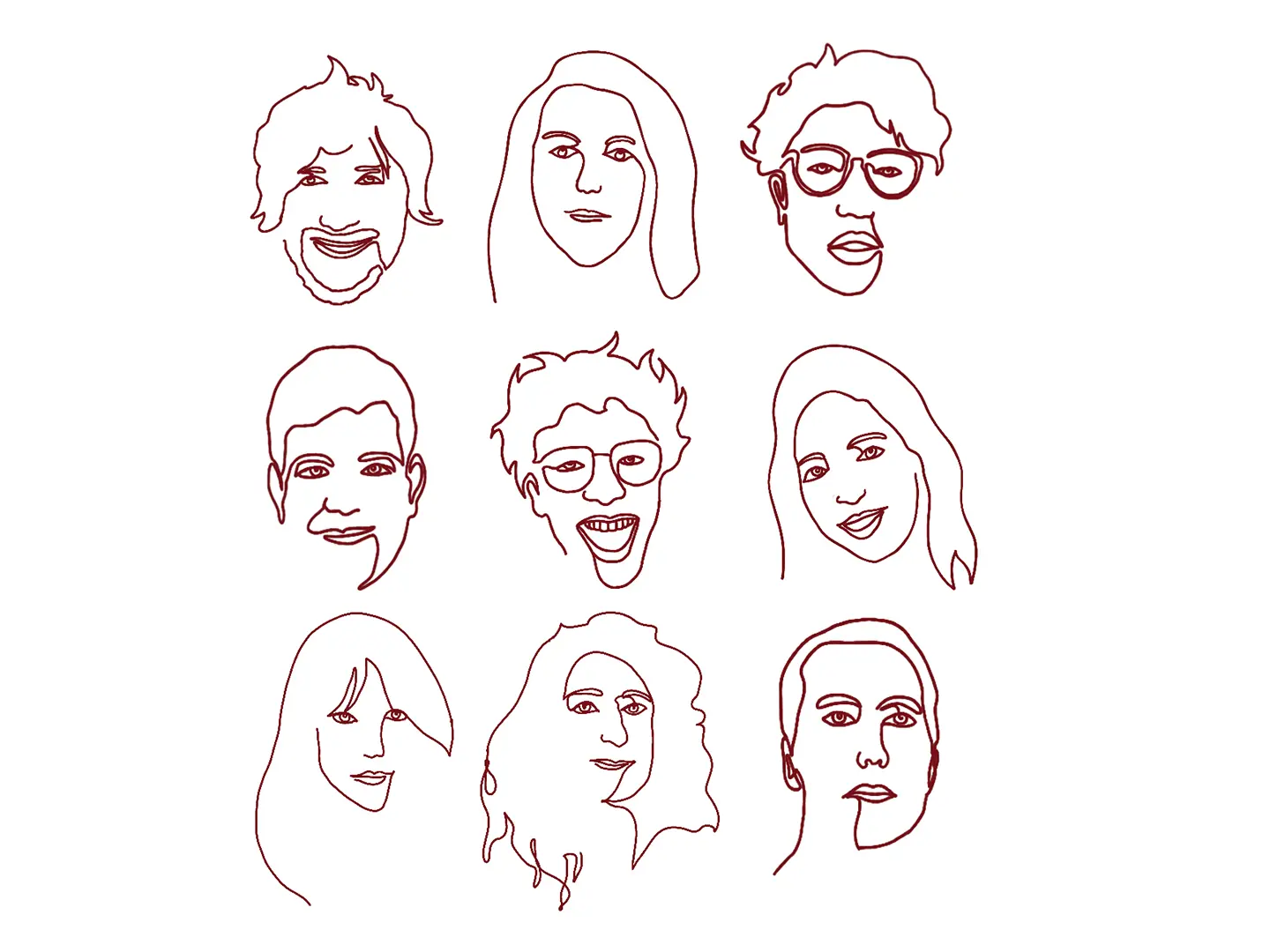
Team EGO.M
Gianfranco Cavaglià: Age doesn’t count when it comes to problems, in fact we can help each other, it depends on mutual willingness. The application of technology allowed us to do something that could not have been achieved previously, we had to think about constraints and possibilities, precision work to refine the design. Intelligent listening and courageous determination are two of the three characteristics of the Samurai. The third, acting, for the good of others, is harder to verify in our society.
EGO.M: Small and timid are adjectives that describe the early stages perfectly, and I would add that we were also a bit scared by the responsibility incurred. But these fears didn’t hold us back, they have always engendered enterprise, perseverance, a thirst for knowledge and enthusiasm. Our legs still shake when we think how important this project was and how crucial it was to pull it off to round off Achille Castiglioni’s oeuvre. We are certainly deeply grateful to the Achille Castiglioni Foundation and to Mr. Cavaglià for the huge faith they had in us and, synecdochally, in younger people and the upcoming generations. It was an act of courage, curiosity and visionary passion.
Gianfranco Cavaglià: The instrument is the interface, the contact, with the hand and, vice versa, the fingers are the interface with the instrument and, generally, three fingers are involved in holding it. This was the starting point, then we perfected the design of the section, and therefore the non-functional model, created with the involvement of the late Master Pierluigi Ghianda.
EGO.M: Preserving the trilobate shape was a crucial condition – giving it up would have meant sacrificing the originality of the design. That was something we never contemplated. The design is undoubtedly complicated and this difficulty was one of the reasons why the project lay unfulfilled until now. Keeping to it and producing functional, financially accessible instruments, in a material that justified its use, and adapting it to the mechanisms available on the market, was the most significant part of our contribution to the project.
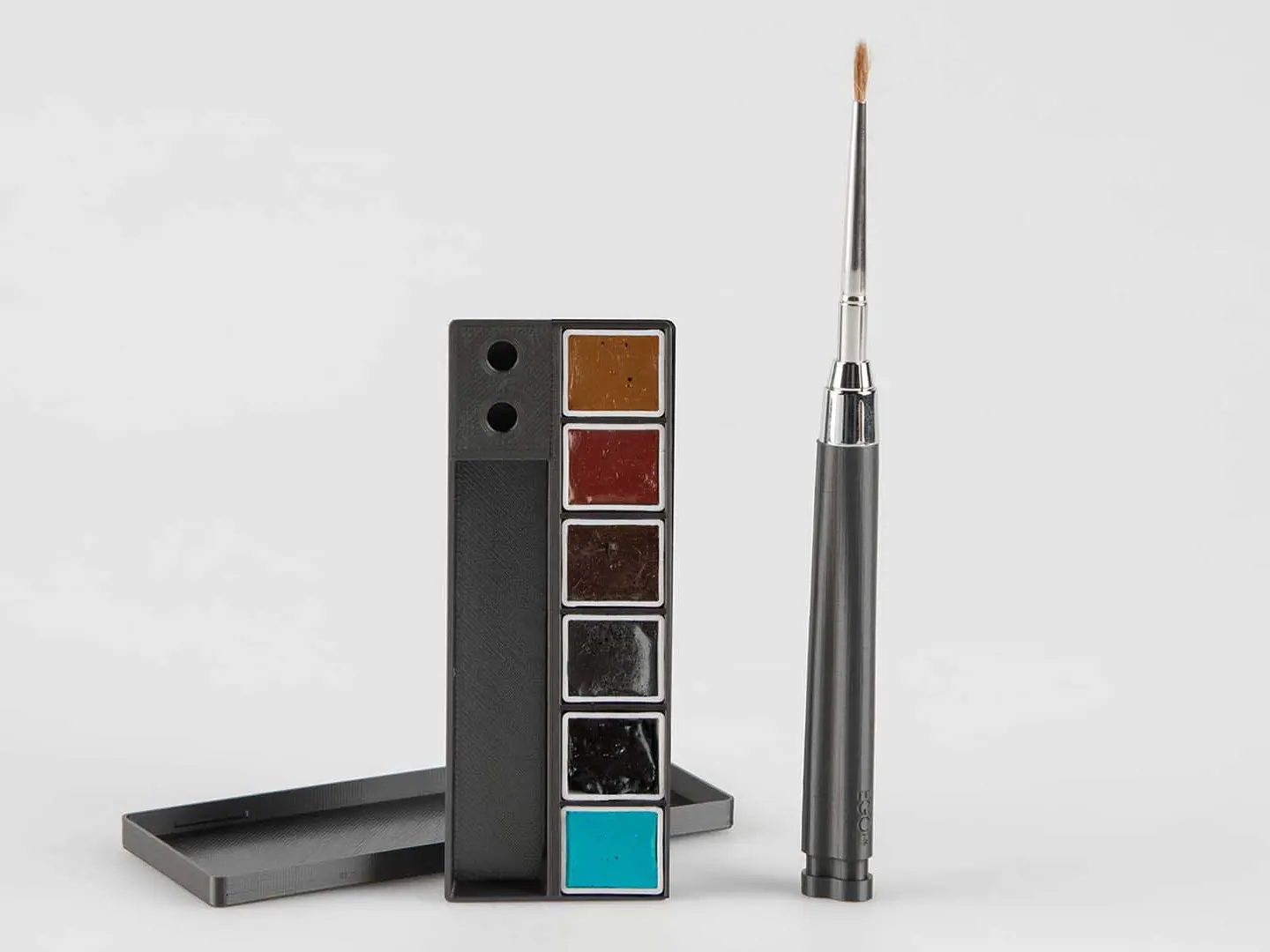
Serendipità Watercolors
Gianfranco Cavaglià: The shape of the section of these writing instruments meant that they would be relatively expensive for something that could not be mass produced and so the project was left to lie. With the arrival of 3D printing, meaning that products could be made directly, doing away with the need for moulds or other expensive methods, we were able to move forward and produce the original project. It’s worth noting that technological innovation has brought about a different outcome than that achieved by industrial production, in which pieces are expected to look a certain way and those that are not up to scratch are discarded. These items, produced through an industrialised process contain small differences in the finish of the surfaces, giving each one its own identity.
EGO.M: We explored various fields and materials and studied the advantages, disadvantages and production characteristics of each of them – resistance, eco-sustainability, equipment, moulds, costs, thermal reactions, friction, use and falls. Using 3D printing for this project also seemed the most correct method given the financial accessibility deriving from the lack of expensive moulds and equipment, the sustainability deriving from the production process, depositing just the necessary material without generating waste, the innovation derived from the fact that a project dating from the start of the millennium could only be produced by skills available in 2021, and lastly because of the intrinsic humanity that it transfers to the objects – every single product has characteristics that mark it out from all the others, a long, slender “scar” that is always in the same position, while differing in texture from object to object.