In partnership with MiCodmc, a selection of establishments ripe for discovery during the 63rd edition of the Salone del Mobile.Milano, from 8th to 13th April
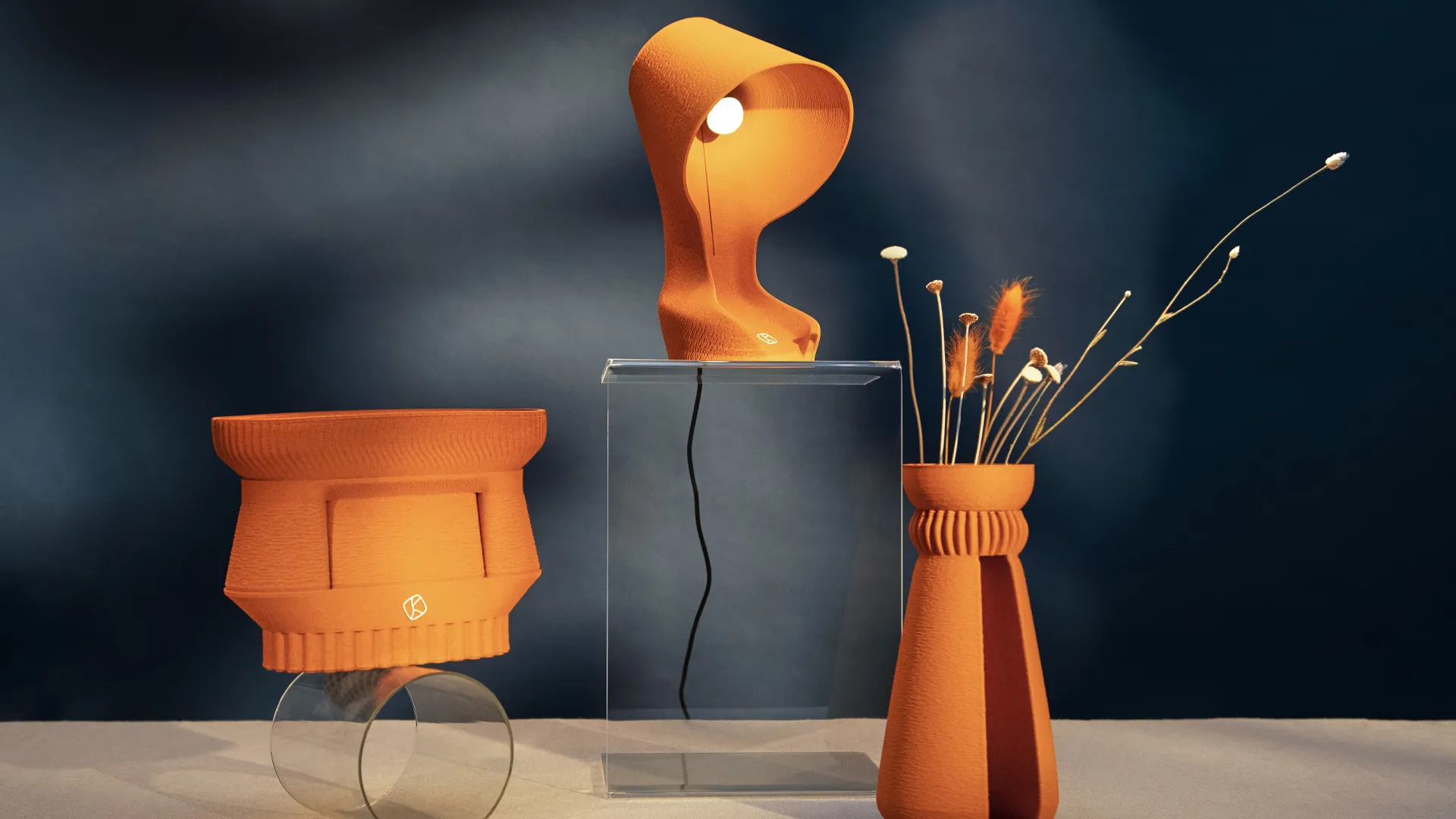
Krill Design, Ribera collection, photo courtesy
Smoothing the transition towards a circular economy, for a future in which sustainable practice, geared to a zero-impact lifestyle, is the norm. Their Ohmie lamp was shortlisted for the 2022 ADI Index. A conversation with Martina Lamperti, Circular Economy Manager at Krill Design
Krill are small crustaceans, rather like shrimps, at the bottom of the marine seafood chain, living in swarms. The concept behind Krill Design is the capillary diffusion of hubs - “Krill points” – up to the coming together of production and end consumer. 3D printing has taken hold and there are so many hubs we can count on. For example: if we wanted to set up our own printing point in France for printing with our material, we could propose a partnership by triggering a virtuous circle with other 3D printing hubs already up and running in that particular region.
Yack (Di Maio) and I met at the Faculty of Architecture at Milan Polytechnic University. Neither of us took architecture any further after we left, but we set up our studio with the idea of designing and then producing our products using 3D printing. We started printing for other people and that’s how Ivan (Calimani) came across us and contacted us – of the three of us, he’s the one with the best entrepreneurial nous. He was looking for people who knew how to design in this particular field.
At the time, he was developing a material deriving from potato peel with a company, and needed someone who could test the materials. That sparked our synergy.
In those days, we didn’t have the know how we have now: we couldn’t create a material that could actually be used, and the project remained on stand-by. The research required such a lot of effort and we were self-financing at the time, so the first material we actually managed to create was derived from the peel of oranges used for juicing at Autogrill.
Yes, it was Autogrill themselves that became interested after a pitch. That then led to the joint idea for a successful collaboration, which culminated in the Was Orange project for sugar sachet holders in some of their outlets.
We were contacted by the San Pellegrino company and carried out the Sicily (R)evolution project, consisting of a tray, a glacette and a table lamp. That’s how it works with companies – either they find you or you manage to make contact with them. There are also companies that scout in order to fulfil their own requirements.
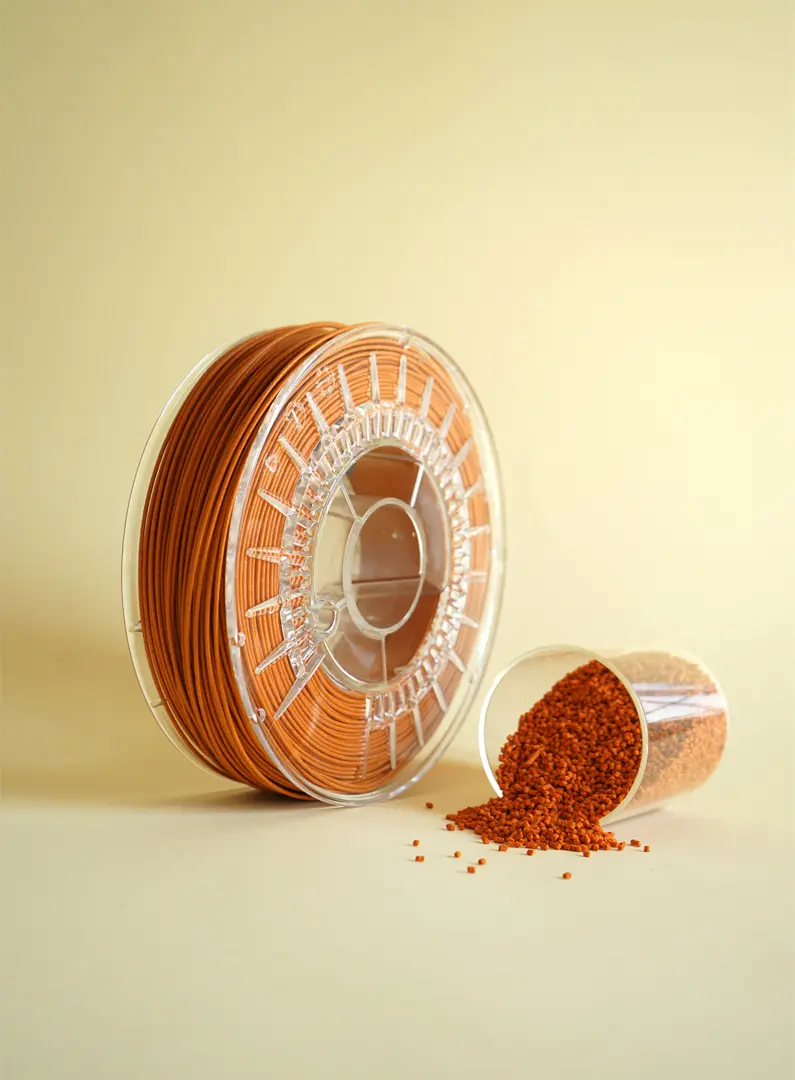
Krill Design, Rekrill Orange Bobine, photo courtesy
We were already familiar with polymers. There were already “enriched” materials such as Woodfill, which is a PLA with added recycled wood fibres, and others that use metals. The basic bioplastic that we employ is PHB, which is biodegradable and compostable, unlike the more frequently-used PLA.
So far, we’ve developed three materials from three different lots of waste: orange, coffee and lemon. We are looking for companies that can offer us a certain sort of waste product. This might derive from chocolate, tomatoes or even from limoncello (not to be confused with lemon, because of its alcoholic content), to carry through circular economy projects.
It’s split into four stages: dried orange – which we call "pastazzo", from the pastazzo to orange powder (this stage is known as “micronisation”). The micronised orange then goes through a compounding process from which orange granules, known as “pellets ”, are obtained. Lastly, the pellets are heated and placed inside an extruder from which the filament we 3D print with is obtained.
We’re not a BeCorp yet, it’s a complicated process, but we are part of the BeCorp NetZero 2030 programme.
Handling everything internally makes us unique. At the moment there are companies that produce biomaterials but stop at sales. We not only produce the biomaterials, we also deal with the finished product. In order to increase the scalability of our business model, we decided to take on the consumer market a year ago, and therefore the end client. We are now making products that we put on sale on our website.
We are three people who complement each other. I (Martina Lamperti) am the Circular Economy Manager and I manage projects for companies; Ivan Calimani is the CEO - Circular Economy Visionary, Entrepreneur; and Yack di Maio is the R&D Manager, managing the materials side, the printing and the research involved with upgrading the printers.
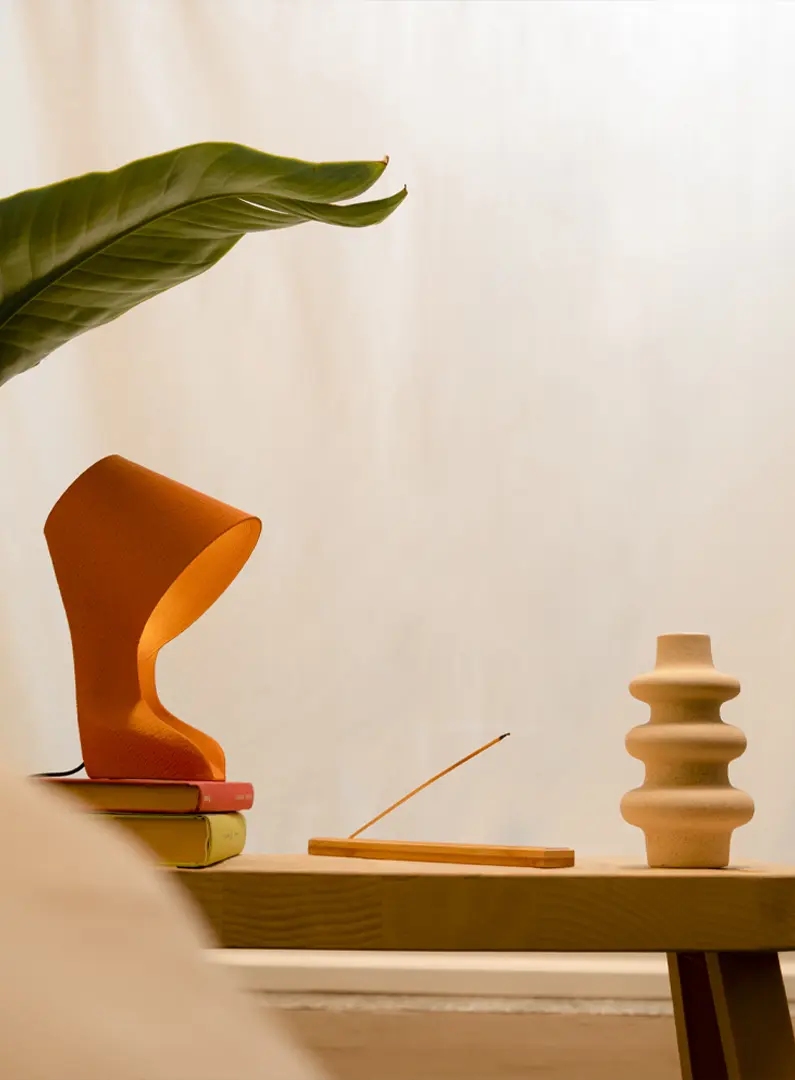
Krill Design, Ohmie the Orange lamp, photo courtesy
Initially all we knew about materials was what we’d learned during our university studies. We had no chemical skills and we had to rely on external consultants.
Developing a new material now takes between two and 4 months, whereas it took nearly a year when we first started.
We decided to enter Ohmie, because it was our flagship product, launched through a crowdfunding campaign in 2021: we sold 600 lamps in one month! When nobody knows you that’s quite an achievement. The other products were a long way off at that time.
Yes, in late 2022 we received the Best Performer for Circular Economy Services award and were recognised as an example of sustainability by the World Economic Forum.
At the moment we’re using organic waste, plant waste, such as fruit, vegetables and cereals. It’s important that they include waste containing starches, sugars, cellulose or lignin, fibres. We then carry out tests on the different types of waste and identify the most suitable ones.
The way we work is “zero waste” – our production doesn’t generate any waste.
If for example a piece doesn’t work, we shred it and feed it back into the material creation process. Our products can be disposed of in organic waste or, better still, returned to us for reuse.
Largely through internally-managed social activities. There are now 10 permanent staff, along with a couple of interns who still collaborate with us even though they’ve completed their internships.
There are lots of things in our printers … The advantage of 3D printing is being able to experiment – you don’t have to make expensive moulds for just a few pieces.
We will be bringing a new collection to Milan, which might just include a lamp … no spoilers for now, though!
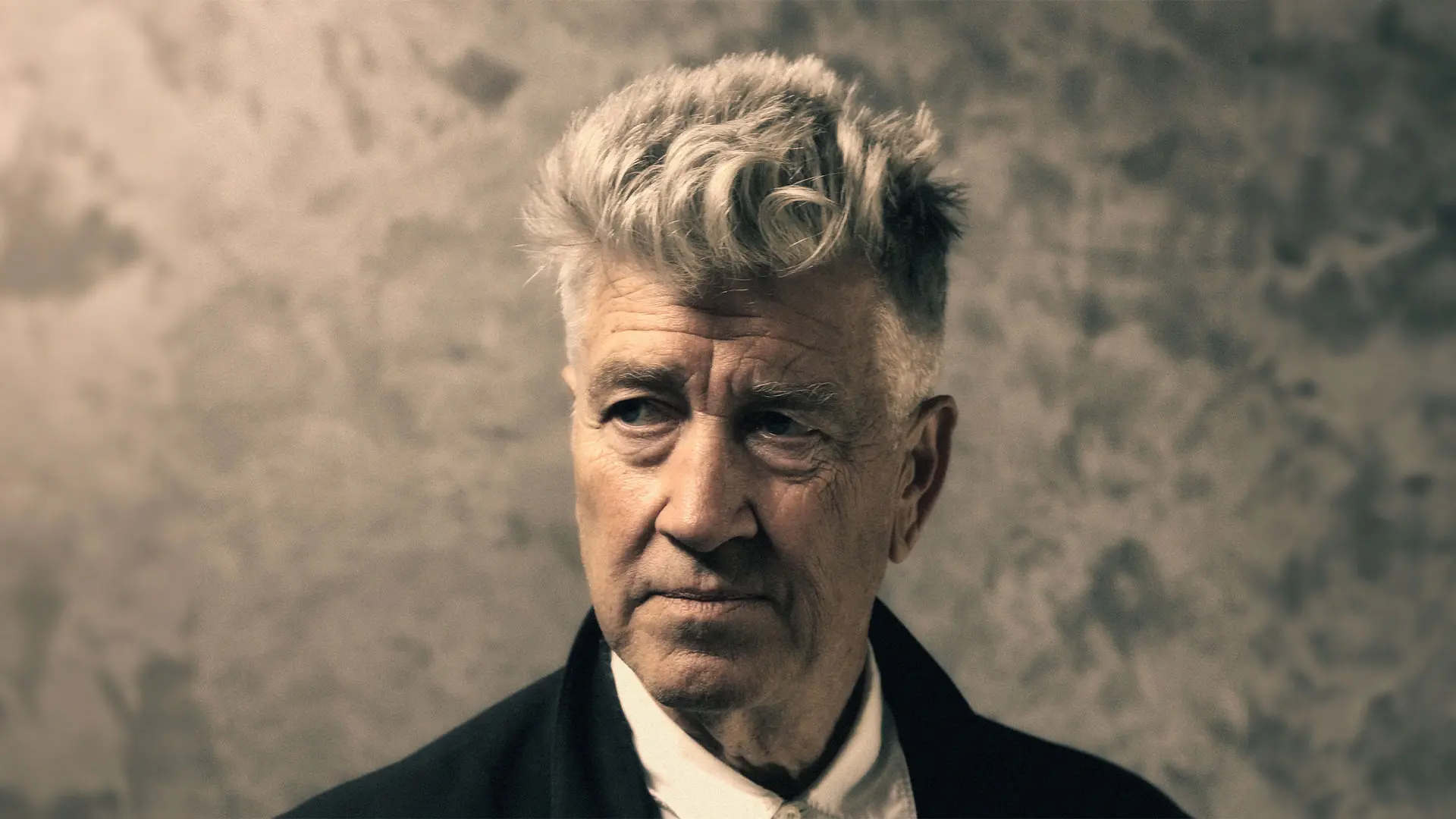
In memoriam: David Lynch
The American director has left us at the age of 78. The Salone del Mobile.Milano had the honor of working with him during its 62nd edition, hosting his immersive installation titled “A Thinking Room”. An extraordinary journey into the depths of the mind and feelings. His vision will continue to be a source of inspiration.